Syringe pumps are designed to ensure precise and controlled delivery of fluids or medications by employing several mechanisms and features that work together.
Here’s how syringe pumps achieve this level of accuracy and control:
- Microstepping or Stepper Motor Control: Many syringe pumps use microstepping or stepper motor control systems. These systems allow for highly accurate and precise movement of the syringe plunger. The stepper motor divides the plunger movement into small steps, with each step representing a known volume. This precise control ensures that the fluid is delivered at the programmed rate.
- Flow Rate Calibration: Before operation, syringe pumps are often calibrated to ensure that the actual flow rate matches the programmed flow rate. This calibration process involves measuring the volume of fluid delivered for a certain number of motor steps, allowing the pump to adjust for any deviations.
- Linear Syringe Plunger Movement: Syringe pumps are designed to maintain a linear relationship between the motor steps and the volume of fluid dispensed. This linearity ensures that the delivered volume matches the programmed volume accurately.
- Real-Time Feedback: Many syringe pumps are equipped with real-time feedback mechanisms, such as optical encoders or position sensors, to constantly monitor the position of the syringe plunger. This feedback system can detect any deviations from the intended position and make immediate adjustments to maintain accuracy.
- Pressure and Occlusion Sensing: To prevent issues like occlusions or blockages in the tubing, syringe pumps often have pressure sensors that monitor the resistance encountered by the fluid. If an occlusion is detected, the pump can halt the infusion, sound an alarm, or take corrective action.
- Air Bubble Detection: Air bubbles can disrupt the accuracy of fluid delivery. Syringe pumps may be equipped with air bubble detection systems that trigger alarms or corrective actions when bubbles are detected in the syringe or tubing.
- Safety Alarms and Alerts: Syringe pumps include alarms and alerts to notify operators of any issues or deviations from the programmed parameters. These warnings can indicate problems like empty syringes, end of infusion, or system errors.
- Closed-Loop Control: Some advanced syringe pumps offer closed-loop control, which means they continuously compare the actual delivery with the programmed parameters and make real-time adjustments to maintain accuracy.
- Anti-Siphoning Mechanisms: Syringe pumps may include anti-siphoning features to prevent unwanted fluid flow when the pump is turned off or the system is depressurized.
- Data Logging and Reporting: Many syringe pumps can log data related to the infusion, including flow rates, volumes delivered, and any alarms. This data can be used for quality control, compliance, and research purposes.
- User Interface: Syringe pumps have user-friendly interfaces that allow operators to set and monitor parameters. The interface often displays real-time information, such as the current flow rate, volume delivered, and any alarms.
- Repeatability and Stability: The materials and components used in syringe pumps are selected for their stability, low friction, and resistance to wear. This ensures that the pump’s performance remains consistent over time.
By incorporating these features and mechanisms, syringe pumps can deliver fluids or medications with a high degree of precision and control, making them valuable tools in medical, laboratory, and industrial settings where accurate and reliable fluid delivery is critical.
What are the factors that should be considered when selecting a syringe pump for a specific application?
Selecting the right syringe pump for a specific application requires careful consideration of several factors to ensure that the pump meets the needs and requirements of the task at hand.
Here are key factors to consider:
- Fluid Type: Determine the type of fluid you will be dispensing. Some syringe pumps are better suited for delivering specific types of fluids, such as viscous or abrasive liquids, volatile chemicals, or biological samples. Ensure that the pump materials and design are compatible with the fluid.
- Required Flow Rate: Identify the desired flow rate for your application. Different syringe pumps have varying flow rate capabilities, and it’s crucial to select one that can achieve the required delivery rate.
- Volume and Syringe Size: Consider the volume of fluid to be delivered and choose an appropriately sized syringe. Syringe pumps are compatible with a range of syringe sizes, so select one that matches your volume requirements.
- Accuracy and Precision: Evaluate the level of accuracy and precision needed for your application. Some syringe pumps offer higher levels of accuracy, especially in research or medical applications, where precision is critical.
- Infusion Mode: Determine whether you require continuous infusion, intermittent bolus delivery, or other infusion modes. Some syringe pumps offer flexibility in this regard, while others are designed for specific infusion types.
- Safety Features: Assess the safety features offered by the syringe pump, such as occlusion detection, air bubble detection, and alarms. The presence of safety mechanisms China Syringe Pumps manufacturers is particularly important in medical applications.
- User Interface: Evaluate the user interface of the syringe pump. Is it easy to program and operate? Look for a user-friendly interface that aligns with the skill level of the operators.
- Data Logging and Connectivity: Consider whether data logging and connectivity options are necessary for your application. These features are valuable for research and quality control, allowing you to record and analyze infusion data.
- Compatibility: Ensure that the syringe pump is compatible with the tubing, connectors, and other accessories required for your application. Some syringe pumps have specific requirements for tubing or connectors.
- Mounting and Portability: Determine whether the pump needs to be mounted on a stand, IV pole, or another support structure, or if it should be portable. Consider the physical setup and space constraints in your facility.
- Power Source: Evaluate the power source of the syringe pump. Does it need to be powered by electricity, or should it have a battery for use in mobile or field applications? Ensure reliable power sources are available.
- Compliance and Certification: In medical or regulated environments, check if the syringe pump complies with relevant industry standards and regulations, such as FDA requirements for medical devices.
- Budget: Consider the budget constraints for your application. Syringe pump prices vary based on their features and capabilities, so balance your requirements with your budget.
- Service and Support: Research the manufacturer’s reputation for customer support and availability of service or repairs. Ensure that you can access technical assistance when needed.
- Application-Specific Requirements: Tailor your choice to any unique requirements of your application. For example, research applications may require compatibility with specific software for experimental control.
By carefully evaluating these factors, you can choose the most suitable syringe pump for your specific application, ensuring accurate and controlled fluid delivery while meeting your operational and budgetary needs.
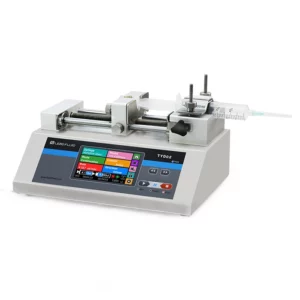